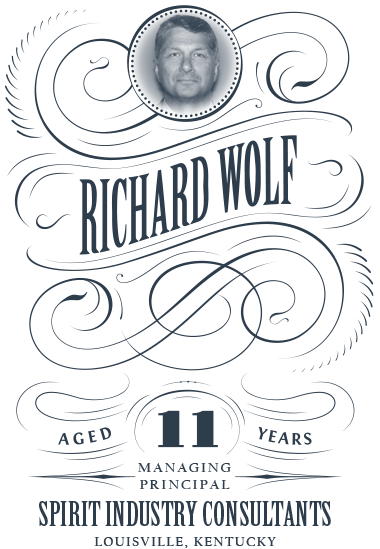
My first call has always been to Rich at Top Shelf Logistics. Secure in the knowledge that he would take point assessing, developing a plan and optimizing my supply chain freed me up to attend to other pressing matters. Rich has helped me to save millions of dollars while profoundly improving service and visibility – from dock management, to headcount rationalization, to finding the right truck at the right time/price. He is the real deal, and his team of professionals at Top Shelf Logistics have what it takes to exceed all of your expectations for a full service 3rd Party Logistics provider.